Технологический процесс изготовления автомобильных листовых рессор
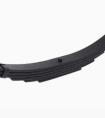
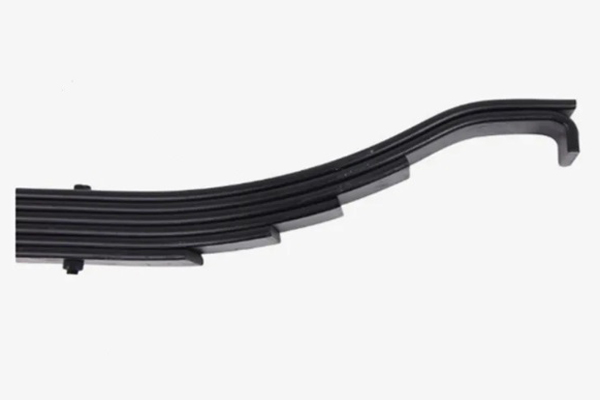
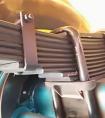
Название продукта: | Технологический процесс изготовления автомобильных листовых рессор |
Ключевые слова: | Автомобильные листовые рессоры, листовые пружины, листовые рессоры, листы листовых рессор |
Промышленность: | Механические и электрические - Станкостроение, машиностроение и производство оборудования |
Ремесла: | листовой металл - Все виды резки |
Материал: | Подшипниковая сталь/рессорная сталь |
Производители перерабатывающей промышленности
- Есть производители 32 , которые предлагают похожую продукцию
- Есть производители 162 , которые предоставляют эту технологию обработки
- Есть производители 61 , которые предоставляют эту услугу по обработке материалов
- Есть производители 139 , которые предоставляют услуги по обработке в этой отрасли
Подробная информация о продукте
Автомобильные листовые рессоры (также известные как листовые пружины) являются ключевыми несущими и амортизирующими элементами в традиционных системах подвески транспортных средств. Их технологический процесс сложен и предъявляет строгие требования, а основная задача заключается в достижении высокой прочности, высокой усталостной долговечности и хороших упругих свойств.
Обычно используются высокопрочные горячекатаные рулоны пружинной стали или мерные прямые полосы, такие как 60Si2MnA, 50CrVA, 55Cr3, серии SUP и т. д. Материал должен соответствовать строгим стандартам химического состава и механических свойств.
Проверенное сырье из пружинной стали разрезается дисковой или ленточной пилой. Возможна лазерная или гидроабразивная резка, но это дороже. Этап резки должен обеспечивать точность длины и качество торцевой поверхности (перпендикулярность, плоскостность), а также уменьшать заусенцы.
Разрезанные стальные полосы нагреваются до температуры аустенизации для подготовки к горячей формовке. Этот процесс требует строгого контроля температуры и времени нагрева (обычно около 900–950 °C, в зависимости от материала), чтобы избежать перегрева, пережога или обезуглероживания.
Нагретые стальные полосы помещаются в роликовую ковочную машину и прокатываются в листы листовой рессоры с заданной кривизной (завитком) и переменным сечением (основная рессора) или постоянным сечением (вспомогательная рессора). Это ключевой этап для получения требуемой жесткости и распределения напряжений.
Сформованные листы листовой рессоры, все еще находящиеся в аустенитном состоянии, быстро переносятся в масляную закалочную ванну для погружного охлаждения, чтобы получить высокотвердую мартенситную структуру, которая закладывает основу для последующего отпуска для получения высокой прочности и высокой упругости.
Закаленные листы листовой рессоры нагреваются до определенной температуры (обычно около 400–500 °C, в зависимости от материала и требований), выдерживаются в течение достаточного времени, а затем охлаждаются (обычно на воздухе). Снимаются закалочные напряжения, повышается ударная вязкость и пластичность, и достигаются необходимые комплексные механические свойства листовой рессоры.
Отожженные листы листовой рессоры подаются в проходную или подвесную дробеструйную машину, где поверхность листовой рессоры бомбардируется высокоскоростным потоком дроби, создавая полезный слой остаточных сжимающих напряжений и улучшая микроструктуру поверхности. Это один из самых важных процессов для повышения усталостной долговечности листовой рессоры.
В завитках основных листов рессор просверливаются или расширяются отверстия, чтобы обеспечить точность размеров отверстий под штифты и шероховатость поверхности. Не завитые концы могут быть подвергнуты снятию фасок, шлифовке и другим операциям для удаления заусенцев и улучшения сборки.
С помощью пресса предварительной нагрузки (гидравлического или механического) отдельные листы листовой рессоры (или иногда несколько листов в сборе) помещаются в зажим и несколько раз (например, 2-3 раза) подвергаются нагрузке, превышающей расчетную полную нагрузку, чтобы вызвать пластическую деформацию. После снятия нагрузки достигается требуемая положительная высота дуги, что улучшает распределение напряжений и межслойное трение во время работы автомобильной листовой рессоры и повышает усталостную долговечность.
Несколько листов листовой рессоры (основные и вспомогательные листы) укладываются по порядку и скрепляются центральным болтом или хомутом (обратным зажимом). Между листами наносится смазка или устанавливаются антифрикционные прокладки/ползунки для уменьшения межслойного трения, износа и шума.
Для обеспечения долговечности листовой рессоры в суровых условиях обычно используется покраска, запекание, порошковое покрытие или цинковое хромирование поверхности листовой рессоры.
Перед поставкой листовые рессоры также проходят выборочную проверку готовой продукции, чтобы гарантировать соответствие размеров и качества продукции требованиям заказчика.
Производство автомобильных листовых рессор — это сложный процесс, объединяющий материаловедение, пластическую обработку, термообработку, обработку поверхности и точный контроль. Каждый этап тесно связан и совместно определяет прочность, упругость, усталостную долговечность и износостойкость конечного продукта. По мере того, как автомобильная промышленность предъявляет все более высокие требования к безопасности, комфорту, снижению веса и долговечности, технология обработки листовых рессор также постоянно развивается и оптимизируется. Строгий контроль качества и постоянные инновации являются ключом к обеспечению соответствия листовых рессор строгим требованиям современных автомобилей.
Обычно используются высокопрочные горячекатаные рулоны пружинной стали или мерные прямые полосы, такие как 60Si2MnA, 50CrVA, 55Cr3, серии SUP и т. д. Материал должен соответствовать строгим стандартам химического состава и механических свойств.
Проверенное сырье из пружинной стали разрезается дисковой или ленточной пилой. Возможна лазерная или гидроабразивная резка, но это дороже. Этап резки должен обеспечивать точность длины и качество торцевой поверхности (перпендикулярность, плоскостность), а также уменьшать заусенцы.
Разрезанные стальные полосы нагреваются до температуры аустенизации для подготовки к горячей формовке. Этот процесс требует строгого контроля температуры и времени нагрева (обычно около 900–950 °C, в зависимости от материала), чтобы избежать перегрева, пережога или обезуглероживания.
Нагретые стальные полосы помещаются в роликовую ковочную машину и прокатываются в листы листовой рессоры с заданной кривизной (завитком) и переменным сечением (основная рессора) или постоянным сечением (вспомогательная рессора). Это ключевой этап для получения требуемой жесткости и распределения напряжений.
Сформованные листы листовой рессоры, все еще находящиеся в аустенитном состоянии, быстро переносятся в масляную закалочную ванну для погружного охлаждения, чтобы получить высокотвердую мартенситную структуру, которая закладывает основу для последующего отпуска для получения высокой прочности и высокой упругости.
Закаленные листы листовой рессоры нагреваются до определенной температуры (обычно около 400–500 °C, в зависимости от материала и требований), выдерживаются в течение достаточного времени, а затем охлаждаются (обычно на воздухе). Снимаются закалочные напряжения, повышается ударная вязкость и пластичность, и достигаются необходимые комплексные механические свойства листовой рессоры.
Отожженные листы листовой рессоры подаются в проходную или подвесную дробеструйную машину, где поверхность листовой рессоры бомбардируется высокоскоростным потоком дроби, создавая полезный слой остаточных сжимающих напряжений и улучшая микроструктуру поверхности. Это один из самых важных процессов для повышения усталостной долговечности листовой рессоры.
В завитках основных листов рессор просверливаются или расширяются отверстия, чтобы обеспечить точность размеров отверстий под штифты и шероховатость поверхности. Не завитые концы могут быть подвергнуты снятию фасок, шлифовке и другим операциям для удаления заусенцев и улучшения сборки.
С помощью пресса предварительной нагрузки (гидравлического или механического) отдельные листы листовой рессоры (или иногда несколько листов в сборе) помещаются в зажим и несколько раз (например, 2-3 раза) подвергаются нагрузке, превышающей расчетную полную нагрузку, чтобы вызвать пластическую деформацию. После снятия нагрузки достигается требуемая положительная высота дуги, что улучшает распределение напряжений и межслойное трение во время работы автомобильной листовой рессоры и повышает усталостную долговечность.
Несколько листов листовой рессоры (основные и вспомогательные листы) укладываются по порядку и скрепляются центральным болтом или хомутом (обратным зажимом). Между листами наносится смазка или устанавливаются антифрикционные прокладки/ползунки для уменьшения межслойного трения, износа и шума.
Для обеспечения долговечности листовой рессоры в суровых условиях обычно используется покраска, запекание, порошковое покрытие или цинковое хромирование поверхности листовой рессоры.
Перед поставкой листовые рессоры также проходят выборочную проверку готовой продукции, чтобы гарантировать соответствие размеров и качества продукции требованиям заказчика.
Производство автомобильных листовых рессор — это сложный процесс, объединяющий материаловедение, пластическую обработку, термообработку, обработку поверхности и точный контроль. Каждый этап тесно связан и совместно определяет прочность, упругость, усталостную долговечность и износостойкость конечного продукта. По мере того, как автомобильная промышленность предъявляет все более высокие требования к безопасности, комфорту, снижению веса и долговечности, технология обработки листовых рессор также постоянно развивается и оптимизируется. Строгий контроль качества и постоянные инновации являются ключом к обеспечению соответствия листовых рессор строгим требованиям современных автомобилей.
Похожие продукты
ЕщеАнализ технологии механической обработки стальных анкерных плит
- Ремесла : механическая обработка - Фрезерование или фрезерование на станке с ЧПУ
- Материал : углеродистая сталь
Броня конусной дробилки
- Ремесла : -
- Материал :
Какие технологические процессы используются при изготовлении корпусов осевых вентиляторов?
- Ремесла : листовой металл - сварка
- Материал : углеродистая сталь
Прецизионная обработка U-образных стальных профилей для строительных конструкций
- Ремесла : штамповка - Обычное тиснение
- Материал : Алюминий
Индивидуальное изготовление сварных H-образных балок S355JR для строительных проектов
- Ремесла : листовой металл - сварка
- Материал : углеродистая сталь
Калибраторы для буровых установок в нефтедобыче
- Ремесла : механическая обработка - Пятиосевая обработка
- Материал : легированная сталь
Токарно-фрезерная обработка толстостенных фланцев и дефектоскопия
- Ремесла : механическая обработка - Токарная и фрезерная обработка
- Материал : легированная сталь
Инновационная технология скашивания: преодоление узкого места технологии рассеивания тепла высокой плотности
- Ремесла : Обработка поверхности - другой
- Материал : легированная сталь
Больше продуктов
ЕщеАнализ технологии механической обработки стальных анкерных плит
- Ремесла : механическая обработка - Фрезерование или фрезерование на станке с ЧПУ
- Материал : углеродистая сталь
Броня конусной дробилки
- Ремесла : -
- Материал :
Какие технологические процессы используются при изготовлении корпусов осевых вентиляторов?
- Ремесла : листовой металл - сварка
- Материал : углеродистая сталь
Прецизионная обработка U-образных стальных профилей для строительных конструкций
- Ремесла : штамповка - Обычное тиснение
- Материал : Алюминий
Индивидуальное изготовление сварных H-образных балок S355JR для строительных проектов
- Ремесла : листовой металл - сварка
- Материал : углеродистая сталь
Калибраторы для буровых установок в нефтедобыче
- Ремесла : механическая обработка - Пятиосевая обработка
- Материал : легированная сталь
Токарно-фрезерная обработка толстостенных фланцев и дефектоскопия
- Ремесла : механическая обработка - Токарная и фрезерная обработка
- Материал : легированная сталь
Инновационная технология скашивания: преодоление узкого места технологии рассеивания тепла высокой плотности
- Ремесла : Обработка поверхности - другой
- Материал : легированная сталь