Технологический процесс изготовления станины токарного станка
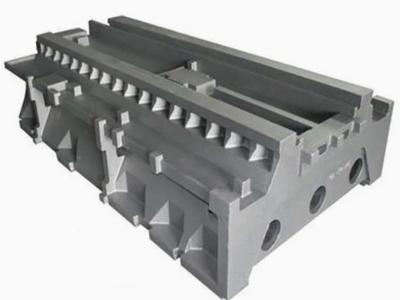
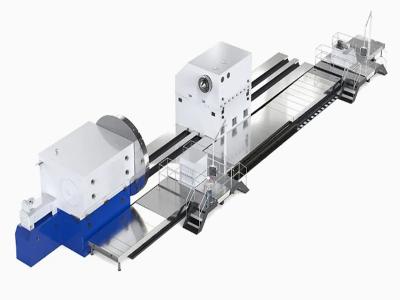
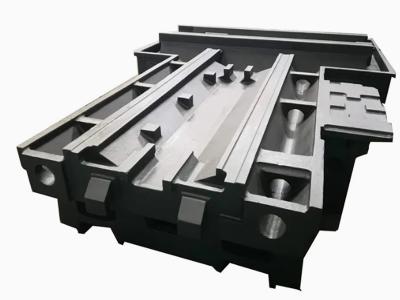
Название продукта: | Технологический процесс изготовления станины токарного станка |
Ключевые слова: | Технологический процесс изготовления станины токарного станка, процесс литья станины токарного станка, черновая обработка станины токарного станка, обработка поверхности станины токарного станка |
Промышленность: | Механические и электрические - Станкостроение, машиностроение и производство оборудования |
Ремесла: | кастинг - другой |
Материал: | Карбид |
Производители перерабатывающей промышленности
- Есть производители 59 , которые предлагают похожую продукцию
- Есть производители 149 , которые предоставляют эту технологию обработки
- Есть производители 113 , которые предоставляют эту услугу по обработке материалов
- Есть производители 137 , которые предоставляют услуги по обработке в этой отрасли
Подробная информация о продукте
Технологический процесс изготовления станины токарного станка включает в себя несколько этапов, направленных на обеспечение точности, прочности и стабильности станины для удовлетворения потребностей высокоточной обработки на токарном станке. Ниже представлено описание основных технологических процессов и ключевых технических моментов обработки станины токарного станка, составленное на основе имеющейся информации:
1. Выбор материала
- Используемые материалы: Станины токарных станков обычно изготавливаются из высокопрочного чугуна (например, HT250 или HT300), благодаря его хорошей виброустойчивости, жесткости и износостойкости. В некоторых высокоточных станках могут использоваться чугун с шаровидным графитом или сварные конструкции из стальных листов.
- Причины: Чугун обладает отличными литейными свойствами и способностью к гашению вибраций, что позволяет ему выдерживать силы резания и вибрации; стальные конструкции используются для облегчения веса или при особых конструктивных требованиях.
2. Литье (или сварка)
- Процесс литья:
- Проектирование пресс-формы: Изготовление прецизионных песчаных или металлических форм в соответствии с чертежами станины, обеспечивающих точность размеров и формы отливки.
- Плавление и заливка: Плавление чугуна с использованием индукционной печи средней частоты, контроль химического состава (например, содержания углерода и кремния), заливка должна производиться при равномерной температуре для предотвращения дефектов, таких как пористость и усадка.
- Охлаждение и очистка: После охлаждения отливки производится пескоструйная или дробеструйная очистка для удаления песка и окалины с поверхности.
- Процесс сварки (при использовании стальной конструкции):
- Использование высокопрочных стальных листов, разрезанных по форме, для сборки каркаса станины путем сварки.
- Необходима термообработка для снятия сварочных напряжений и обеспечения стабильности конструкции.
3. Черновая обработка
- Цель: Удаление припуска с поверхности отливки или сварной конструкции, предварительное формирование.
- Оборудование: Крупногабаритные портальные фрезерные станки, расточные станки или обрабатывающие центры с ЧПУ.
- Процесс:
- Обработка базовой поверхности: Определение базовой поверхности станины (например, нижней поверхности или поверхности направляющих) для обеспечения точности позиционирования при последующей обработке.
- Фрезерование: Черновое фрезерование основных плоскостей станины (например, поверхности установки направляющих, нижней поверхности) с оставлением припуска на обработку (обычно 2-5 мм).
- Сверление: Обработка монтажных отверстий, каналов для охлаждающей жидкости и других конструктивных элементов, обеспечение точности расположения отверстий.
4. Термическая обработка
- Старение:
- Естественное старение: Размещение отливки на несколько месяцев или год для снятия внутренних напряжений под воздействием окружающей среды, низкая стоимость, но длительный период.
- Искусственное старение: Снятие остаточных напряжений путем вибрационного старения или термического старения (нагрев до 500-600°C с последующим медленным охлаждением), повышение стабильности размеров.
- Цель: Уменьшение деформации при последующей обработке и эксплуатации, обеспечение долговременной стабильности станины.
5. Чистовая обработка
- Оборудование: Высокоточные портальные фрезерные станки с ЧПУ, шлифовальные станки или станки для шлифования направляющих.
- Процесс:
- Обработка поверхности направляющих: Поверхность направляющих станины токарного станка является ключевым элементом, требующим высокой прямолинейности и чистоты поверхности (Ra0.8-1.6). Обычно используется прецизионное фрезерование с последующим шлифованием или непосредственная обработка на станке для шлифования направляющих.
- Контроль плоскостности: Погрешность плоскостности поверхности направляющих должна контролироваться в пределах 0.01-0.02 мм/м.
- Чистовая обработка системы отверстий: Растачивание или развертывание отверстий для установки шпиндельной бабки, задней бабки и т.д., обеспечение соосности и точности расположения.
- Поверхностное упрочнение (опционально): Высокочастотная закалка поверхности направляющих или нанесение пластикового покрытия (например, ленты PTFE), повышение износостойкости и предотвращение заедания.
6. Обработка поверхности
- Полировка или покраска: Полировка или покраска нефункциональных поверхностей антикоррозийной краской для улучшения внешнего вида и коррозионной стойкости.
- Канавки для смазки направляющих: Обработка канавок для смазки или установка системы смазки для обеспечения длительной и плавной работы направляющих.
7. Контроль и калибровка
- Контрольное оборудование: Трехкоординатные измерительные машины, лазерные интерферометры, уровни и т.д.
- Содержание контроля:
- Геометрическая точность: Проверка параллельности, плоскостности и прямолинейности поверхности направляющих.
- Точность позиционирования: Проверка допусков на расположение и соосность системы отверстий.
- Качество поверхности: Измерение шероховатости и твердости поверхности.
- Калибровка: При обнаружении отклонений используется шабрение (ручное или механическое) для незначительной корректировки поверхности направляющих, обеспечивая точность.
8. Сборка и отладка
- Сборка: Установка шпиндельной бабки, задней бабки, суппорта и других компонентов на станину, регулировка точности сопряжения компонентов.
- Отладка: Проведение пробного запуска, проверка вибрации, шума и точности обработки станины, при необходимости тонкая настройка направляющих или повторное шабрение.
Ключевые технические моменты
- Выбор параметров резания: В зависимости от материала и этапа обработки, рациональный выбор скорости резания, подачи и глубины резания, чтобы избежать чрезмерного износа инструмента или деформации заготовки.
- Контроль точности: Точность обработки поверхности направляющих напрямую влияет на производительность токарного станка, необходимо строго контролировать плоскостность и прямолинейность.
- Снятие напряжений: Термическая обработка после литья или сварки является важным этапом для предотвращения деформации при длительном использовании.
- Выбор оборудования: Для обработки крупногабаритных станин необходимо использовать станки с ЧПУ с большим ходом (например, портальные фрезерные станки) для обеспечения эффективности и точности обработки.
Предыдущая статья : Основные моменты при установке центраторов
Следующая статья : Вращающийся управляемый центратор
Похожие продукты
ЕщеАнализ технологии механической обработки стальных анкерных плит
- Ремесла : механическая обработка - Фрезерование или фрезерование на станке с ЧПУ
- Материал : углеродистая сталь
Броня конусной дробилки
- Ремесла : -
- Материал :
Индивидуальное изготовление сварных H-образных балок S355JR для строительных проектов
- Ремесла : листовой металл - сварка
- Материал : углеродистая сталь
Какие технологические процессы используются при изготовлении корпусов осевых вентиляторов?
- Ремесла : листовой металл - сварка
- Материал : углеродистая сталь
Калибраторы для буровых установок в нефтедобыче
- Ремесла : механическая обработка - Пятиосевая обработка
- Материал : легированная сталь
Токарно-фрезерная обработка толстостенных фланцев и дефектоскопия
- Ремесла : механическая обработка - Токарная и фрезерная обработка
- Материал : легированная сталь
Прецизионная обработка U-образных стальных профилей для строительных конструкций
- Ремесла : штамповка - Обычное тиснение
- Материал : Алюминий
Инновационная технология скашивания: преодоление узкого места технологии рассеивания тепла высокой плотности
- Ремесла : Обработка поверхности - другой
- Материал : легированная сталь
Больше продуктов
ЕщеАнализ технологии механической обработки стальных анкерных плит
- Ремесла : механическая обработка - Фрезерование или фрезерование на станке с ЧПУ
- Материал : углеродистая сталь
Броня конусной дробилки
- Ремесла : -
- Материал :
Индивидуальное изготовление сварных H-образных балок S355JR для строительных проектов
- Ремесла : листовой металл - сварка
- Материал : углеродистая сталь
Какие технологические процессы используются при изготовлении корпусов осевых вентиляторов?
- Ремесла : листовой металл - сварка
- Материал : углеродистая сталь
Калибраторы для буровых установок в нефтедобыче
- Ремесла : механическая обработка - Пятиосевая обработка
- Материал : легированная сталь
Токарно-фрезерная обработка толстостенных фланцев и дефектоскопия
- Ремесла : механическая обработка - Токарная и фрезерная обработка
- Материал : легированная сталь
Прецизионная обработка U-образных стальных профилей для строительных конструкций
- Ремесла : штамповка - Обычное тиснение
- Материал : Алюминий
Инновационная технология скашивания: преодоление узкого места технологии рассеивания тепла высокой плотности
- Ремесла : Обработка поверхности - другой
- Материал : легированная сталь